Home
zurück
Eigenbau eines Faltbootes - Seite 4
Direkt zu Seite... 1 / 2 / 3 / 4 / 5 / 6 / 7 / 8
zurück
Wie ich bereits erwähnt habe ändert sich die Beschreibung hier hinsichtlich der Leisten für die Senten und damit auch der Verbindunsstücke aus Aluminium. Ich verwende nun Rundhölzer. Dementsprechend müssen die Aufnahmen in den Spanten auch rund gefeilt werden. Links und rechts neben dem Kiel verlaufen die Bodensenten. Am Bug habe ich sie mit einem Winkel befestigt. Das Ende der Bodensenten sollte man schön rund schleifen, damit später keine Ecken in die Bootshaut drücken.
Die seitlichen Senten habe ich mittels Sperrholzbrettchen zu Bordwänden verbunden. Bordwände haben den Vorteil, dass sie das Boot besser versteifen, dafür sind sie etwas sperriger vom Packmaß. Stöße gegen die Senten werden besser aufgefangen und mindern die Bruchgefahr.
Foto 
Am Bug beginnend habe ich die Rundhölzer auf der Innenseite etwas angeschliffen, damit sie plan auf den Sperrholzplatten (hellblau) aufliegen können. Die Sperrholzplatten habe ich erst nach dem Verschrauben der Senten in ihre entgültige Form gebracht. Die Position der Senten auf den Sperrholzplatten ergibt sich aus deren Verlauf vom Bug zu den Ecken von Spant 1. Diesen Verlauf habe ich auf den Sperrholzplatten aufgezeichnet und nach dem Vorbohren die Senten unter Verwendung von wasserfestem Holzleim angeschraubt. Die Schrauben, die ich verwendet habe, waren alle zu lang, sie haben auf der anderen Seite der Senten wieder herausgeschaut. Ich habe sie mit dem Winkelschleifer, den ich mit einer Lamellen-Schleifscheibe bestückt habe, bündig abgeschliffen.
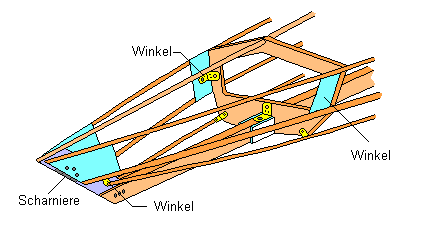 Anschließend sägt man den Überstand der Sperrholzplatte oben und unten ab und schleift die Kante rund, bis sie der Rundung der Senten entspricht. Danach die Platte vorn parallel zum Bugsteven abgesägt. Der Anfang der Senten wird schräg abgeschliffen, damit auch hier später keine Ecken und Kanten in die Bootshaut drücken.
Nun legt man beide Bordwandteile genau passend aufeinander (sie sollten eigentlich genau gleich sein) und bohrt die Löcher für die Scharniere. Die von mir verwendeten Modelle aus Edelstahl sind aufgeklappt 7 x 8 cm groß und haben in jedem Flügel jeweils 3 Löcher zum Verschrauben. Zum Festschrauben habe ich Maschinenschrauben und Kontermuttern verwendet, Gewindeüberstand habe ich abgeschliffen. Als nächstes wird die eine der fast fertigen Bordwände an den Bug und Spant 1 angesetzt und die Bohrlöcher für die Befestigung der Scharniere am Bugsteven werden angezeichnet. Nach dem Bohren werden beide Bordwandhälften mit Maschinenschrauben und Kontermuttern verschraubt, Gewindeüberstand wird wieder abgeschliffen.
Dort, wo die Senten am Spant 1 anliegen, habe ich auf der Innenseite 10 cm abgeschliffen, vorgebohrt, dann 10 cm breite Sperrholzbrettchen angeleimt und angeschraubt, den Gewindeüberstand abgeschliffen und anschließend die Brettchen auf Bordwandhöhe gekürzt und die Kanten rundgeschliffen.
Diese Brettchen stoßen nun, wenn man das Boot seitwärts biegt, gegen den Spant. Dadurch wird dem Boot sehr viel Steifigkeit gegeben.
Damit die Bordwände nicht von den Spanten wegklappen können, habe ich mittig auf diesen Brettchen Winkel angeschraubt. Durch den Spant habe ich Löcher in der Größe M8 gebohrt. Nun kann man die Bordwände mit einem durch Spant und Winkel gesteckten Splint fixieren. Als Splint verwende ich Ringschrauben in der Größe M6, am Ring habe ich eine Schlaufe aus Gummischnur angeknotet, die über den Gewindestift gezogen wird, damit die Ringschraube nicht herausfallen kann. Ebenso bin ich mit den Bodensenten verfahren.
Foto 
Bei den Senten habe ich Rundholzstäbe aus massiver Kiefer mit einem Durchmesser von 20 mm gewählt. Als Verbinder verwende ich Aluminiumrohr mit einem Außendurchmesser von ebenfalls 20 mm. Bei den Bodensenten, die lediglich eine formgebende Rolle haben und keinen starken Belastungen ausgesetzt sind, habe ich mich für Rundholzleisten aus Kiefer sowie Aluminiumrohr mit 15 mm Durchmesser entschieden. Ich hoffe, dadurch das Gesamtgewicht des Bootes etwas zu reduzieren.
Die Verbindung selbst ist denkbar einfach: Die Rundholzstäbe sind an den Enden soweit verjüngt, dass ein etwa 16 cm langes Stück Aluminiumrohr 8 cm weit aufgeschoben und festgeklebt werden kann. Weitere 8 cm des Verbindungsrohres bleiben frei. Das Sentenstück, dass nun hineingesteckt werden soll, wird am Ende so weit verjüngt, dass ohne zu klemmen oder stark zu reiben hinein passt. Wichtig ist, zu bedenken, dass das Holz noch lackiert wird und der Zapfen dadurch wieder etwas dicker wird.
Es ist ratsam, das Aluminiumrohr vor dem zersägen in die einzelnen Rohrelemente etwas zu biegen, so das die einzelnen Verbinder später leicht gekrümmt sind und so mithelfen, die Bootsrundung zu formen.
Des weiteren ist es sinnvoll, die Verbinder am jeweils vorn liegenden Segment der Senten zu befestigen. Eine leichte Kante zwischen den Segmenten läßt sich nicht ganz vermeiden, liegt diese jedoch in Fahrtrichtung gesehen am hinteren Ende des Segmentes, so ragen eventuelle Erhebungen der Bootshaut nicht so hervor, dass sie gegen die Fahrtrichtung weisen und so Reibungshindernissen werden, die eine Beschädigung der Bootshaut forcieren.
|